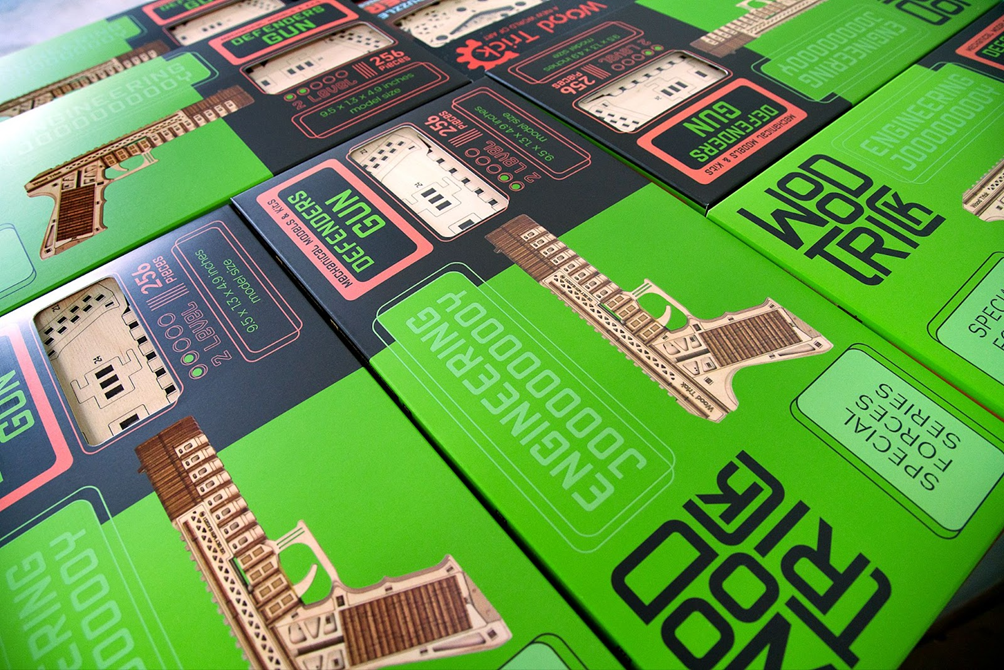
From Concept to Creation: How 3D Wooden Puzzles Are Made
3D wooden puzzles are a fun and engaging challenge for all ages. These intricate, three-dimensional creations aren’t just enjoyable to put together — they also highlight the craftsmanship and artistic design behind them. Ever wondered how they’re made? Let’s walk through the step-by-step process, from the initial concept to the final product.
Designing the Puzzle
It always starts with an idea. A 3D wooden puzzle can take the form of anything — from a simple geometric shape to an intricate model of an animal, vehicle, or famous landmark. Our designers begin by sketching out the pieces and determining how they’ll fit together. They also plan the overall structure, ensuring that the finished puzzle is both visually striking and sturdy enough to hold its shape.
Picking the Right Wood
After finalizing the design, it’s time to choose the perfect wood for the puzzle. Most 3D wooden puzzles are crafted from high-quality hardwoods such as maple or birch, which are prized for their strength, durability, and beautiful grain. To prevent the pieces from warping or changing shape over time, the wood is kiln-dried to remove excess moisture, ensuring a long-lasting and sturdy final product.
Cutting the Pieces
Now that the design and wood are selected, it’s time to cut the puzzle pieces. A laser cutter is most often used for this, as it can make highly precise cuts for all the intricate shapes. The laser works by focusing a high-powered beam onto the wood, burning through it to create the desired shape. This method provides clean edges and reduces waste, leaving you with high-quality puzzle pieces. There are also a couple of other methods for cutting the pieces:
- Scroll Saw Cutting: This method uses a scroll saw, a tool with a thin, back-and-forth blade, to cut out detailed shapes. It offers more control and precision than laser cutting but takes a bit more time.
-
CNC Routing: CNC stands for Computer Numerical Control, and this method uses a computer-controlled machine to carve out the pieces. It’s ideal for intricate designs and ensures high precision.
Sanding and Smoothing
After the pieces are cut, they need to be sanded and smoothed to remove any rough edges or imperfections. This step is essential because smooth surfaces ensure the puzzle pieces fit together perfectly. The sanding process can be done using sandpaper, sanding blocks, or even a power sander, depending on the size and complexity of the puzzle.
Finishing the Wood
After sanding, the puzzle pieces are treated to protect the wood and highlight its natural beauty. There are various finishes to choose from, such as oils, waxes, and varnishes, each offering different levels of protection and visual appeal.
-
Oils: Oils like tung or Danish oil penetrate the wood, protecting it while preserving its natural look.
-
Waxes: Waxes, such as beeswax or carnauba wax, create a soft shine and add a protective layer. This option is gentle and ideal for the final touch, as it doesn't alter the appearance or interfere with the puzzle's functionality.
-
Lacquers: Lacquers, including polyurethane, create a tough, moisture-resistant coating. The downside, however, is that varnishes can add extra weight, which may impact the functionality of mechanical puzzles.
The finishing process typically involves applying one or more coats, with light buffing in between, to achieve a smooth, even surface.
Assembly and Quality Control
Before the puzzles are cut, packed, and shipped, our testers assemble each 3D wooden puzzle to ensure all the pieces fit properly and that the final product meets high-quality standards. This step helps identify any issues or defects early, so customers receive a puzzle that’s both impressive and fully functional.
Packaging and Shipping
After the puzzle clears quality control, it’s disassembled, and each piece is carefully packed in a box or protective case. The package usually includes assembly instructions, a picture of the finished puzzle, and any tools needed, like a small wooden mallet or glue. Once everything is packed up, the puzzle is shipped off to retailers or directly to customers.
Creating a 3D wooden puzzle is all about blending creativity, craftsmanship, and precision. From the initial concept and design to the cutting, sanding, and finishing, every step plays a key role in making a high-quality, fun puzzle. So, the next time you dive into a 3D wooden puzzle, take a second to appreciate the skill and effort behind this cool and engaging hobby.